manual handling risk assessment template
Summary
Download our free manual handling risk assessment template. Perfect for UK workplaces. Easy to use and customisable.
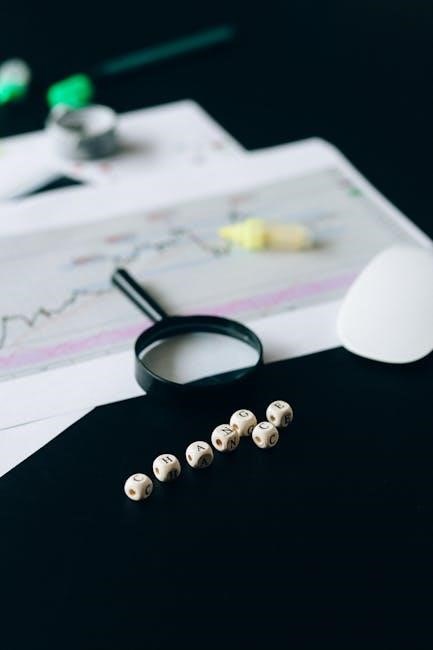
A manual handling risk assessment template is a structured tool designed to identify, evaluate, and mitigate risks associated with manual handling tasks in the workplace.
A manual handling risk assessment is a systematic process used to identify and evaluate the risks associated with manual handling tasks in the workplace. These tasks, which involve lifting, carrying, pushing, or pulling objects, can pose significant risks to employees, leading to injuries and musculoskeletal disorders. The assessment process helps employers and safety managers pinpoint potential hazards, such as heavy loads, awkward postures, or repetitive movements, and determine the likelihood of harm. By conducting a thorough risk assessment, organizations can implement targeted control measures to reduce injuries and create a safer working environment. This process is not only a legal requirement in many regions but also a cornerstone of workplace health and safety management.
Why Manual Handling Risk Assessment is Important for Workplace Safety
Manual handling risk assessments are essential for ensuring workplace safety and reducing the likelihood of injuries and musculoskeletal disorders. Manual handling tasks, such as lifting, carrying, and pushing, are common in many industries and can pose significant risks to employees if not managed properly. Conducting a risk assessment helps employers identify potential hazards, evaluate their severity, and implement control measures to mitigate risks. This not only protects workers’ health but also reduces the financial and operational impacts of workplace accidents. Additionally, it demonstrates compliance with health and safety regulations and fosters a culture of safety within the organization. Regular assessments ensure a proactive approach to preventing injuries and enhancing overall workplace well-being.
How to Conduct a Manual Handling Risk Assessment
Conducting a manual handling risk assessment involves identifying hazards in tasks like lifting, carrying, pushing, or pulling objects. Start by observing employees to spot unsafe practices. Use tools like the Manual Handling Assessment Charts (MAC) to evaluate tasks based on factors such as object weight, distance carried, and posture. Assess the risk level using a scoring system or matrix to determine the likelihood and severity of harm. Implement control measures like mechanical aids, training, and adjusting workloads. Consider workplace conditions, such as environment and layout, and document the assessment, including tasks, risks, and controls. Regular reassessments and employee training are crucial to maintaining safety and compliance.
Identifying Hazards in Manual Handling Tasks
Identifying hazards in manual handling tasks is the first step in a risk assessment. It involves observing how tasks are performed and recognizing potential risks. Hazards may include heavy or awkwardly shaped objects, repetitive movements, or poor posture. Environmental factors like uneven surfaces, limited space, or extreme temperatures can also contribute to risks. Tools like the Manual Handling Assessment Charts (MAC) help evaluate tasks based on factors such as weight, distance carried, and posture. Hazards can also arise from individual differences, such as physical capabilities or pre-existing health conditions. Documenting these hazards helps prioritize risks and inform control measures. For example, tasks like lifting heavy boxes or handling hot materials require special attention to prevent injuries. Regular monitoring ensures hazards are not overlooked and adjustments are made as needed.
Evaluating the Risk Level of Manual Handling Activities
Evaluating the risk level of manual handling activities involves assessing the likelihood and potential impact of injuries. This step uses tools like risk matrices or scoring systems to categorize risks as low, medium, or high. Factors such as task frequency, weight, posture, and individual capabilities are considered. For example, lifting heavy objects overhead may pose a higher risk than carrying lighter loads at waist height. Legal standards, such as AS 45001, provide guidelines for evaluating risks. The assessment also considers environmental factors like floor surfaces or lighting. By prioritizing high-risk tasks, employers can focus on implementing effective control measures. This evaluation ensures that risks are managed proportionally, reducing the likelihood of workplace injuries.
Implementing Control Measures to Reduce Risks
After identifying and evaluating risks, implementing control measures is crucial to minimize injuries. Start by introducing mechanical aids, such as lifting equipment or conveyors, to reduce manual effort. Ensure proper workplace layout and ergonomic design to eliminate awkward postures. Provide training on safe manual handling techniques, focusing on proper lifting and carrying methods. Regularly monitor tasks and update controls as needed. Encourage worker participation in identifying and implementing solutions. Personal Protective Equipment (PPE) may also be necessary in certain situations. Document all control measures and ensure compliance with legal standards. Regular reviews and updates to these measures are essential to maintain a safe working environment and reduce the likelihood of manual handling injuries.
Monitoring and Reviewing the Risk Assessment Process
Monitoring and reviewing the risk assessment process ensures that control measures remain effective and relevant over time. Regularly inspect manual handling tasks and assess whether existing controls are reducing risks as intended. Seek feedback from workers to identify any new hazards or issues that may have arisen. Review the risk assessment after any workplace changes, such as new equipment or procedures, or following incidents or near misses. Update the risk assessment document accordingly and communicate changes to all relevant staff. This ongoing process helps maintain a safe working environment, ensures compliance with regulations, and adapts to evolving workplace conditions and practices.
Elements of a Manual Handling Risk Assessment Template
Key components include task descriptions, risk evaluation systems, control measures, documentation, and responsibilities to ensure workplace safety and compliance.
Description of Manual Handling Tasks and Workplace Conditions
This section provides a detailed overview of the specific manual handling tasks being assessed, including how they are performed and by whom. It requires observing and analyzing tasks to capture variations in workflow and work demand. Workplace conditions are thoroughly described, covering the environment, layout, and physical factors such as access and egress. The number of employees involved in the task and their roles are noted. Additionally, the systems of work for the activity are listed to ensure a comprehensive understanding of the task’s context. This step is crucial for identifying potential hazards and ensuring the assessment aligns with the actual work practices and conditions.
Risk Evaluation and Scoring Systems
Risk evaluation and scoring systems are essential for assessing the severity of manual handling risks. These systems often involve assigning scores to factors such as task frequency, weight, and posture to quantify risk levels. For example, tasks requiring repetitive lifting of heavy objects may receive higher scores, indicating greater risk. This step helps prioritize risks and determine the urgency of implementing control measures. Many templates include scoring guidelines aligned with industry standards, such as AS 45001:2018, to ensure consistency and compliance; The scores are used to categorize risks as low, medium, or high, guiding employers in taking appropriate action to mitigate hazards effectively.
Control Measures and Safety Precautions
Control measures and safety precautions are critical for minimizing risks identified during manual handling assessments. These measures may include training employees in proper lifting techniques, using mechanical aids like hoists or trolleys, and ergonomic adjustments to workstations. Additionally, implementing safe work practices, such as task rotation and load redistribution, can reduce strain. Personal protective equipment (PPE) may also be necessary for specific tasks. Regular monitoring ensures these controls remain effective. Customizing control measures to suit workplace conditions is key, as outlined in many templates. Proper documentation of these measures is essential for compliance and accountability, ensuring a safer environment for all employees involved in manual handling tasks.
Documentation and Responsibilities
Documentation is a cornerstone of effective manual handling risk assessments, ensuring transparency and accountability. It involves recording task descriptions, hazard identification, risk evaluation, and implemented control measures; Responsibilities are clearly defined, with employers accountable for conducting assessments and providing safe systems of work. Supervisors must ensure tasks are performed safely, while employees are responsible for following guidelines and reporting hazards. Regular reviews and updates to the documentation are essential to maintain relevance and compliance. Proper record-keeping facilitates audits and demonstrates adherence to health and safety regulations, fostering a culture of accountability and continuous improvement in workplace safety.
Best Practices for Using a Manual Handling Risk Assessment Template
Customize the template for specific tasks, ensure compliance with regulations, involve stakeholders, and regularly review assessments for continuous improvement in workplace safety and efficiency.
Customizing the Template for Specific Workplace Needs
Customizing a manual handling risk assessment template ensures it aligns with the unique demands of your workplace. Start by identifying specific manual handling tasks, such as lifting, carrying, or pushing, and assess the associated risks. Consider the physical environment, including workspace layout, access points, and equipment used. Tailor the template to reflect your organization’s policies, legal requirements, and industry standards. Involve stakeholders, such as employees and health and safety officers, to provide insights into task-specific hazards. Regularly update the template as workplace conditions or tasks evolve. This ensures the assessment remains relevant and effective in mitigating risks and enhancing workplace safety.
Implementing a manual handling risk assessment template is a crucial step toward ensuring workplace safety and reducing injury risks. By identifying hazards, evaluating risks, and applying control measures, organizations can create a safer environment for employees. The next steps involve training staff on proper manual handling techniques and regularly reviewing the risk assessment process. Organizations should also consider seeking professional advice to ensure compliance with health and safety regulations. Continuous monitoring and updates to the risk assessment template will help adapt to changing workplace conditions. Prioritizing manual handling safety not only protects employees but also fosters a culture of safety and responsibility within the organization.
Additional Resources for Manual Handling Risk Assessment
Several free manual handling risk assessment templates are available online, designed to help organizations streamline their safety processes. These resources often include step-by-step guides, hazard identification tools, and risk evaluation matrices; Many templates align with international standards like AS 45001:2018, ensuring compliance and effectiveness. Additionally, Safe Work Method Statements (SWMS) are provided to outline safe practices for manual handling tasks. Some resources also offer accredited training courses in manual handling, fire safety, and workplace health and safety. Regular updates to these tools ensure they reflect the latest safety guidelines and research. Organizations can download and customize these templates to suit their specific needs, enhancing their ability to protect workers and maintain a safe work environment.